Stepweld
TRENCH MESH WELDING PLANTS FROM COIL OR PRE-CUT LENGTHS
STEPWELD series plants produce high-quality welded mesh, characterized by single or double panels (even overlapping), composed of a minimum number of 2 to 8 longitudinal wires whose diameter range may be between 4 and 20 mm.
The cross wire feeds may have a diameter range from 4 to 12 mm and as in the case of the longitudinal wire feeds they can be in the form of of wire coil or pre-cut bars.
Key features:
High productivity: STEPWELD plants guarantee rapid and efficient production, with minimized set-up times.
Reliability and robustness: Built with high-quality materials, STEPWELD plants are designed to last over time and withstand intensive use.
Versatility: STEPWELD models are available in various configurations to meet specific production needs.
Superior quality: The combined action of a series of exclusive devices guarantees a finished product of the highest quality.
Ease of use: STEPWELD plants are easy to configure and use, thanks to an intuitive control system.
Safety: All STEPWELD plants comply with the latest safety regulations.
Available models:
STEPWELD M: For the use of longitudinal and transverse wires made from pre-cut bars.
STEPWELD H: For the use of bars for the longitudinal wires and wire mesh for the transverse wires.
STEPWELD S: For the production of single or double panels with high levels of productivity.
STEPWELD 4S: For the simultaneous production of two identical and overlapping mesh panels, with even higher levels of productivity.
Additional options:
Automatic tying system: Eliminates the need to tie the mesh bundles manually, maximising plant productivity.
Automatic packaging machine: for stacking multiple bundles of tied mesh, increasing the storage area and optimising lifting and evacuation operations.
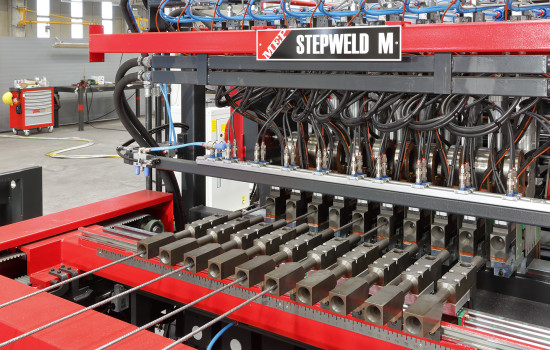
Stepweld M
TRENCH MESH WELDING PLANTS FROM COIL OR PRE-CUT LENGTHS
Feeding:
Pre-straightened and pre-cut bars for both longitudinal and cross wire feeding.
Longitudinal bar insertion:
Manual, semi-automatic, or automatic.
Production process:
Fully automatic (cross wire insertion, mesh forming, storage and evacuation).
Welding unit:
Pneumatic cylinders with software-controlled transformers for uniform current distribution across welding points (number proportional to mesh width).
High productivity:
Suitable for high-volume production of electro-welded mesh.
Maximum mesh width: 1600 mm.
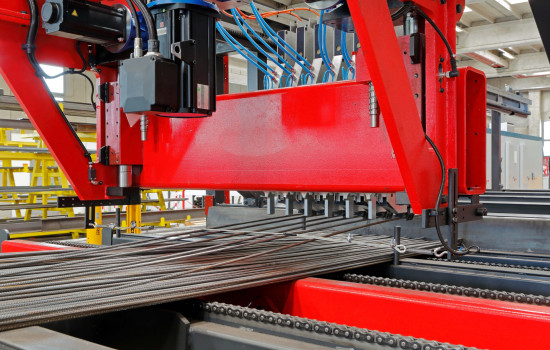
Stepweld H
TRENCH MESH WELDING PLANT FROM COIL OR PRE-CUT LENGTHS
Feeding:
Pre-straightened and pre-cut bars for longitudinal lines.
Coil of wire (round cold drawn or hot rolled,smooth or ribbed) for cross lines (hybrid feeding).
Longitudinal bar insertion:
Manual, semi-automatic, or automatic.
Production process:
Fully automatic (cross wire insertion, mesh forming, storage and evacuation).
Welding unit:
Pneumatic cylinders.
Number of transformers proportional to maximum mesh width for uniform welding.
Software control of welding parameters.
High productivity:
Suitable for high-volume production of electro-welded mesh.
Maximum mesh width: 1600 mm.

Stepweld S
TRENCH MESH WELDING PLANTS FROM COIL OR PRE-CUT LENGTHS
Feeding:
Coil of wire (round cold drawn or hot rolled,smooth or ribbed) for longitudinal and transverse lines.
Product:
Lattice plane girders (not electro-welded mesh) with a maximum of two longitudinal wires.
Production process:
Fully automatic (straightening, positioning, welding, cutting).
Longitudinal wire straightening:
Use of rotors with hard metal parts.
Welding unit:
Pneumatic cylinders and software-controlled transformers.
Panel evacuation and stacking:
Automatic.
High productivity:
Ideal for the production of lattice plane girders, particularly suitable for residential trenches.
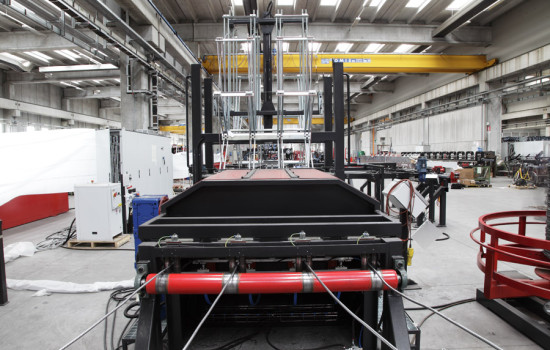
Stepweld 4S
TRENCH MESH WELDING PLANT FROM COIL OR PRE-CUT LENGTHS
High productivity: simultaneous production of 2 overlapping panels.
Double line: 2 separate lines for the formation of cross wires.
Final product: electro-welded mesh with a maximum of 4 and a minimum of 2 longitudinal wires.
Automatic process: fully automatic production after setting parameters.
Efficient welding: welding unit with 2 insertions and a series of opposing welding electrodes.
Reduced footprint: panels with opposite cross wires for more compact stacks.
Unloading: automatic unloading of panels.