GAM
PRE-CAGE FORMING, CAGE ASSEMBLING, CYLINDRICAL OR VARIABLE PILES
GAM HS universal wire mesh welding machines represent the ideal solution for the automatic production of cylindrical and polygonal cages in various shapes and sizes.
Key features:
Flexibility: production of cages with diameters from 200 to 2000 mm and lengths up to 24 m.
High productivity: optimized and continuous work cycle thanks to state-of-the-art drive and control systems.
Impeccable quality: latest generation robotic welding and bar counting system for unparalleled precision.
Versatility: production of cylindrical, square, rectangular, or polygonal cages with various types of longitudinal bars.
Compact configuration: optimized design to reduce footprint and associated costs.
Ease of use: intuitive control system and quick change between different cage types.
Safety: automatic process interruption system for manual insertion of internal reinforcement rings.
Optimal support: synchronized devices for cage support during the forming phase.
Benefits:
Reduced setup times and operating costs.
Production of high-quality cages with uniform welding.
Flexibility to meet the most diverse production needs.
Reduced footprint for easy integration into the production area.
Maximum operator safety.
GAM HS are the ideal choice for manufacturers who require an efficient, versatile and reliable solution for the production of high-quality cages.

Gam 1500 HS
PRE-CAGE FORMING, CAGE ASSEMBLING, CYLINDRICAL OR VARIABLE PILES
Cages of various forms and sizes
Fast and easy configuration
Automatic bushes positioning
The latest generation welding robot
Manual adjustment of welding parameters
Flexible spiral (fixed/variable pitch, adjustable minimum distance)
Electronic control of all machine parameters
Automatic bar counting
Side loading of bars
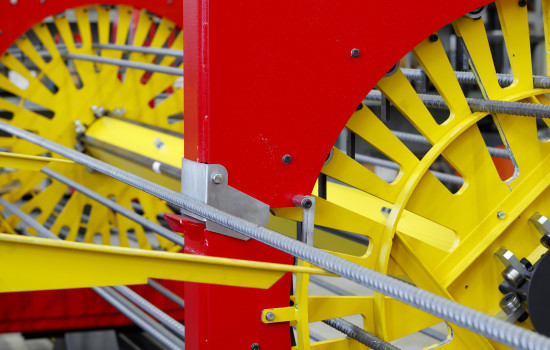
Gam 1500 HS PLUS
PRE-CAGE FORMING, CAGE ASSEMBLING, CYLINDRICAL OR VARIABLE PILES
• Cages of various forms and sizes
• Double welding device
• Spiral with two wires
• Double welding joints on the same wire
• Up to 24 meters length
• Fast and easy configuration
• Automatic bushes positioning
• The latest generation welding robot
• Variable welding pitch control
• Electronic control of all machine parameters
• Automatic bar counting
Request information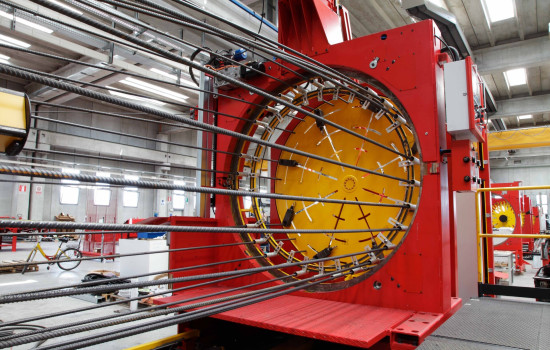
Gam 2000 HS
PRE-CAGE FORMING, CAGE ASSEMBLING, CYLINDRICAL OR VARIABLE PILES
• Cages of various forms and sizes
• Fast and easy configuration
• Automatic bushes positioning
• The latest generation welding robot
• Manual adjustment of welding parameters
• Electronic control of all machine parameters
• Automatic bar counting
• Longitudinally movable pay off on rails for spiral diameter ∅20 mm (#6)
Request information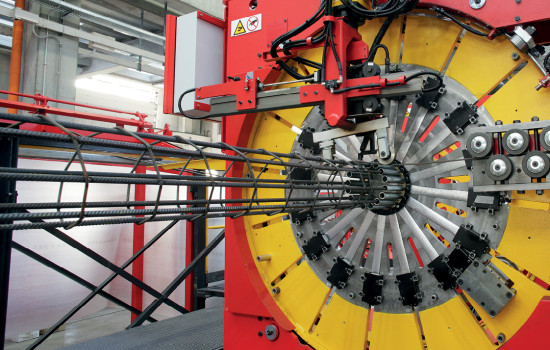
Gam 1500 HS CONIC
GAM 1500 HS CONIC
The universal cages of the GAM HS Conic series are particularly suitable for the production of conical, cylindrical and polygonal cages of various shapes and sizes. It is possible to produce tapered cages with variable circumferences, fully automated. Compactness, productivity and high quality of the fi nished product, are some of the main characteristics of this plants.
Automated circumference setting
The “Master head” is cleverly designed with a device capable of moving the guide bushes radially, based on the cage to be produced. During the translation cycle of the “Master head” and the relative formation of the cage, the guide bushes are automatically positioned so as to be able to create cage sections with different circumferences depending on the pitch and rate of tapering required.
Welding innovation
The welding robot, that bonds the spiral wrap to the longitudinal bars, is able to automatically follow the variations in circumference of the cage to be formed according to the programmed data. In this way it is possible to create cages characterized by different taper angles and diameters in a completely fully automatic mode.
Automatic clamping
An assembly of automatic clamps, positioned on the “fi xed head” dedicated to the fi xing of the longitudinal bars, may be customised in number and size (min/max diameter of the bars to be used).
Automated synchronisation delivers reliable quality
The high quality of the product archiveable is the result of an accurate system of automation that manages the whole production cycle. The robotic welding process and the type of cage to be manufactured, help determine the synchronised rotation speed of all the heads (Fixed, Master and Slave/idle), guaranteeing accurate symmetry of the cages and repeatability, as is required in mass production. The exclusive design of the GAM HS and GAM HS Conic allows the insertion and manual welding of the internal reinforcement/lifting rings, if required, at the programmed distance predetermined in the data entry phase. The process of forming the cage is automatically interrupted at the exact point where it is to be inserted, allowing for quick and easy manual welding, then effortless resumption, back into automatic mode.
Cage support arms
It consists of several devices whose synchronized movement allows the cage to be supported during the cage formation phase. When forming square, rectangular or polygonal shaped cages, they should be equipped by special cup-like attachments (optional) fi tted to these support arms, ensuring constant positive contact with the cage, during rotation. As soon as the cage is completed, the operator gives his consent for the support arms to lower and clear simultaneously, as part of the unloading operation.
MEP World System: total control
The World System, through a “user friendly” interface, allows total control of all the devices of the system, enhancing its performance. Operator panel P.L.C. Industrial MEP composed of:
- LCD screen for displaying all information in a user-friendly graphic form.
- Compact micro controller (“embedded”) with low absorption.
- Input/Output and motion control electronic boards with short circuit prevention system.
World System software
The software specially developed by MEP allows to:
- Program cage production data.
- Templates settings. By entering the dimensional data of the cage (pole diameter, longitudinal diameter, spiral diameter, number of longitudinal bars) the software indicates to the operator which template to use and prepares the machine in the correct mounting position of the longitudinal support bushings.
- Control of all machine parameters.
- Active “diagnostics” system for a constant check of the efficiency of all the devices of the plant.
- Programming of cages with double bar (coupled GAM HS).
- Programming of welding type. For each section it is possible to indicate whether the welding should be continuous (each intersection between longitudinal and spiral) or alternating (each two intersections, each three, ...).
- Programming of the welding time.
- Spiral pitch programming, with the possibility of varying it continuously along the entire length of the cage.
- Intermediate stops programmed (e.g. reinforcing/lifting rings).
- Possibility of loading the cages production data remotely (e.g. offi ce) via RS232 serial port.
- Storage and archiving of data related to work cycles (and generation of daily production statistics (Start, Stop, Alarms, etc.) with the possibility to download data via RS232 serial port.