MRSA
MESH WELDING PLANTS FROM PRE-CUT LENGTHS
Flexibility, productivity, and sturdiness are the hallmarks of the MRSA series plants, designed for the production of welded mesh from pre-cut bars,off-coils, or a combination of both, either cold drawn or hot rolled.
Adaptability to different needs:
• Standard or custom mesh: Ideal for the production of mesh with constant or variable diameters and pitches, meeting a wide range of production needs.
• Wide range of diameters: They work with wire from 4 to 25 mm in diameter.
Complete automation:
• They reduce manual operator intervention thanks to an automated production process.
Cost optimization:
• They allow to reduce industrial costs per ton thanks to the use of a smaller number of machines and operators.
Custom solutions:
• They offer multiple configurations to adapt to the specific production and layout needs of the customer.
• The use of standard modular technologies allows to create a "tailor-made" plant.
Device and accessory combinations:
• The MRSA series allows the integration of a wide range of devices and accessories to further optimize the production process.
The MRSA series plants represent a versatile, efficient, and robust solution for the production of high-quality welded mesh.
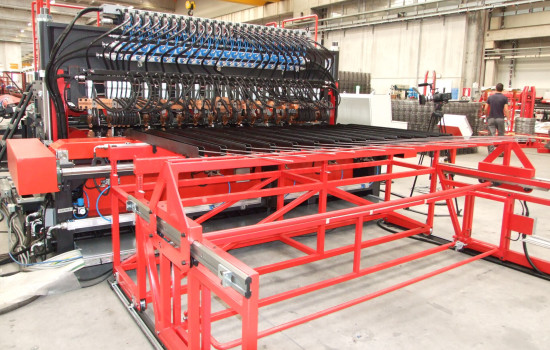
MRSA M
MRSA M (Manual)
MESH WELDING PLANT FROM PRE-CUT LENGTHS
Manual longitudinal bar loading.
Automatic transverse bar feeder.
Automatic panel ejector.
Bridge welding.
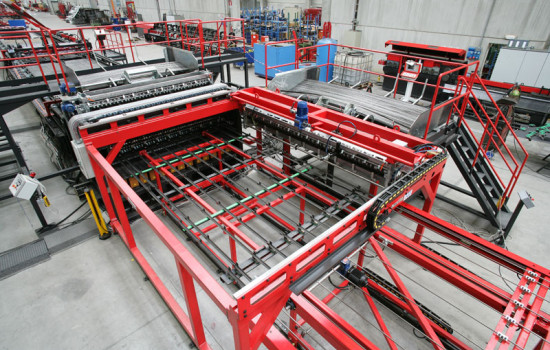
MRSA S
MRSA S (Semi-automatic)
MESH WELDING PLANT FROM PRE-CUT LENGTHS
Semi-automatic longitudinal bar loader: An efficient and safe process.
Automatic transverse bar feeder: Efficient solution for continuous production.
Unloading carriage: For the automatic removal of produced panels.
Stacker: For the automatic stacking of finished panels.
Bridge welding: Ensures uniform weld quality.
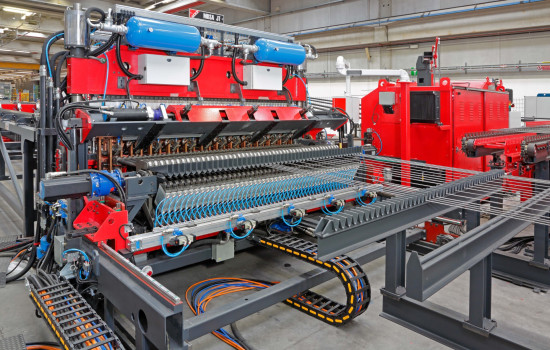
MRSA JT
MRSA JT (Just in Time)
MESH WELDING PLANT FROM PRE-CUT LENGTHS
• Coil feeding: both longitudinal and cross wires fed from coils.
• Rapid mesh size change: automatic and quick mesh size adjustments.
• Multiple wire coils: automatic coil switching for different wire diameters.
• Automatic straightening: two automatic straightening machines for longitudinal and cross wires.
• Automatic cutting and insertion: bars cut and inserted as needed.
• Versatile welding: cross wires can be welded above or below longitudinal wires.
• Automated process: automatic panel collection and evacuation.
• Uniform welding: multiple transformers for even current distribution.
Request information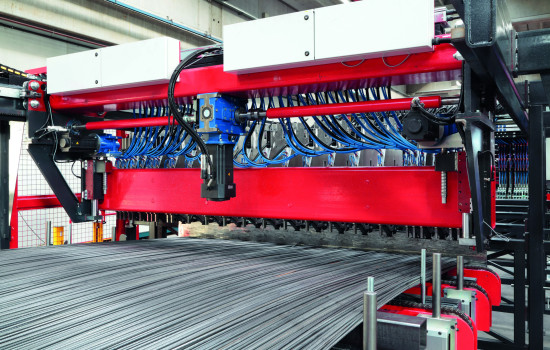
MRSA F
MRSA F (Force)
MESH WELDING PLANT FROM PRE-CUT LENGTHS
Feeding: pre-straightened and pre-cut bars for both longitudinal and cross wires.
High welding force: hydraulic cylinders enable welding of thicker bars (Ø16 mm for both longitudinal and cross wires).
Welding up to Ø25 mm: maximum technological expression for customized meshes of medium and large dimensions.
Uniform welding: one transformer per welding cylinder ensures consistent electrical current at each welding point.
Positioning flexibility: rapid cylinder movement via automatic robot or manual operation.
Automatic insertion: automatic insertion of cross wires, mesh forming, collection, and discharge.
Suitable for structural meshes: ideal for producing complex structural meshes.
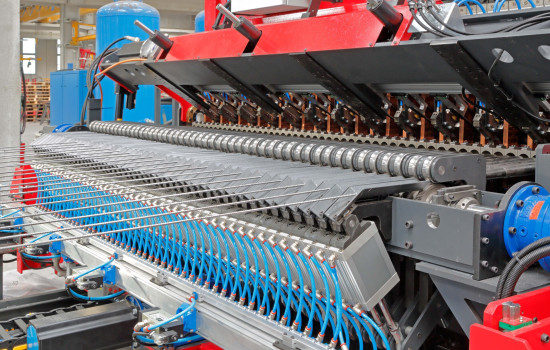
MRSA CL HA
MRSA CL HA (CL+Up and down)
MESH WELDING PLANT FROM PRE-CUT LENGTHS
Hybrid feeding system: pre-cut and pre-straightened longitudinal bars; transverse wire from coil (cold-drawn or hot-rolled, smooth or ribbed). This feeding combination is also called "hybrid".
Versatile welding: cross wires can be welded above or below longitudinal bars without turner stacker device (automatic device for the sequential rotation and stacking produced mesh panels).
Automated processes: automatic straightening, cutting, insertion of cross wires, mesh forming, and panel evacuation.
Flexible longitudinal bar insertion: semi or fully automatic based on customer needs.
Even current distribution: multiple transformers adjusted to mesh width for consistent welding.
Pneumatic welding: welding unit powered by pneumatic cylinders.