MTM
ELECTRO-WELDING TRUSS GIRDER MACHINES
MTM series electro-welded truss plants represent the ideal solution for companies that require efficient and high-quality production. Thanks to their innovative design and the use of cutting-edge technologies, these plants guarantee:
High productivity: MTM plants are able to produce electro-welded trusses quickly and precisely, ensuring high production that meets the needs of even the most productive companies.
Reduced setup times: Changing the truss height is quick and easy, minimizing downtime and maximizing productivity.
Reliability and robustness: Built with high-quality materials and reliable components, MTM plants guarantee a long service life and uninterrupted production.
Flexibility: MTM plants are available in various configurations to meet the needs of every customer. They can be used for the production of standard trusses (same diameter and length) or for processing dimensionally different trusses.
High level of productivity: The MTM 400 version is particularly suitable for companies that require a high level of productivity. It can be integrated with customizable stacking systems that also include automatic tying (optional).
State-of-the-art drive and control system
MTM plants are equipped with a state-of-the-art drive and control system that optimizes the production process and achieves high levels of efficiency. The system completely eliminates manual operations, ensuring a continuous and optimized work cycle.
Superior quality product
MTM plants allow you to obtain a superior quality product thanks to the use of a series of exclusive devices that reduce set-up times and minimize production waste.
Main technical features
Pre-uncoiler unit: uses two straightening groups for the production of "zig-zag" triangles and longitudinal bars. The longitudinal bars can vary the speed or direction of rotation to guarantee the linearity of the truss.
Straightening process: carried out through three rotating "rotor" groups with Widia bushings, adjustable according to the diameter and quality of the bar.
Welding technology: latest generation (controlled profile current) that avoids alterations of the mechanical characteristics of the steel and also guarantees reduced energy consumption.
Advantages:
Increased productivity
Reduced setup times
Improved product quality
Reduced waste
Energy saving
Reliability and robustness
Flexibility
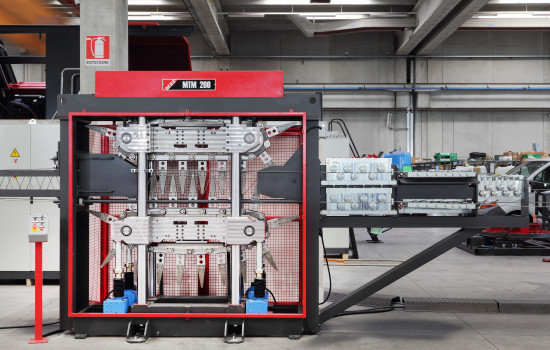
MTM 200
ELECTRO-WELDING TRUSS GIRDER MACHINE
• Constant de-coiling
• Rotors for longitudinal bars
• Straightening the “Zig-zag”
• A single welding unit
• Precision cutting
• Synchronised feeding
• Automatic stacking (automatic vertical or horizontal stacker (optional))
• Automatic tying machines (optional)
• Truss girder turner (optional)
Request information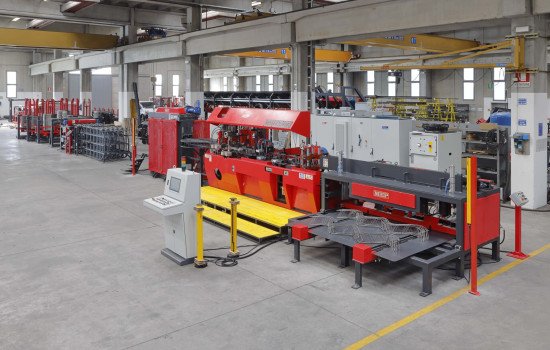
MTM SB 400
ELECTRO-WELDING TRUSS GIRDER MACHINE
• Production of the 2 trusses simultaneously
• Exceptional productivity for serial production and a wide range of trusses
• High productivity with customizable stacking systems
• Drives and controls for high productivity and continuous operation
• Elimination of manual operations
• Exclusive devices for a superior product: fast times, reduced scraps
• 6 straightening units with orthogonal rollers: 2 for “Zig-zag” and 4 for longitudinal wires, with adjustable positioning by diameter and quality
• Constant de-coiling
• The perfect “Zig-zag” triangle
• 2 independent welding units
• Precision cutting
• Synchronised feeding
• Automatic device for shaping and transporting wavy trusses, customisable for different production requirements
• Automatic vertical stacker (optional)
Request information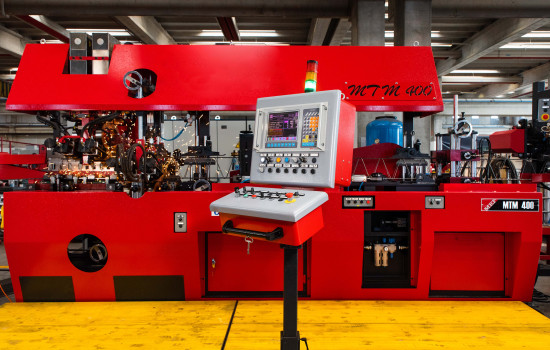
MTM 400
ELECTRO-WELDING TRUSS GIRDER MACHINE
• Constant de-coiling
• Rotors for longitudinal bars
• Straightening the “Zig-zag”
• The height adjustment of the truss
• Two independent welding groups
• Precision cutting
• Synchronised feeding
• Automatic stacking customised to specific production needs
• Automatic tying machines (optional)
• Truss girder turner (optional)
Request information