P - C Weld / Twin Weld
ELECTRO-WELD MESH MACHINES FROM COIL
These machines P-C Weld/Twin Weld are designed for the production of standard electro-welded mesh using coiled wire, both cold drawn, hot rolled and smooth or ribbed. Flexibility, productivity, and robustness are the key features of these models, making them ideal for the production of standard mesh with constant diameters and pitches.
Key advantages:
High customization: various panel or roll stacking, tying, and storage systems can be customized to meet specific production needs.
Wide range of configurations: P-C Weld/Twin Weld are available in various versions with production capacities ranging from single welding units (P-C-Combi Weld) to double units (P-C-Combi Twin Weld). They also offer customizable solutions for minimum/maximum pitches (longitudinal and transverse), mesh dimensions, and strokes per minute.
Cost reduction: process optimization with fewer machines and operators leads to significant cost savings per ton of mesh produced.
Versatility: the multiple versions available allow for adaptation to any production and layout requirement, ensuring maximum flexibility.
Tailor-made solutions: the use of modular and standardized technologies allows for the creation of a customized system based on the customer's specific requirements.
Components and accessories:
Pay-off unit: unwinds the wire from the coils smoothly and controllably, ensuring constant tension during the welding process.
Straightening machines: eliminate any curvature of the wire, ensuring maximum precision in laying and welding.
Welding cages: consisting of electrodes arranged longitudinally and transversally, they generate the welds that join the wires together.
Cutting unit: cuts the mesh into panels or rolls of the desired length.
Stacking and storage systems: automate the movement and positioning of mesh panels or rolls, optimizing workflows and storage of the finished product.
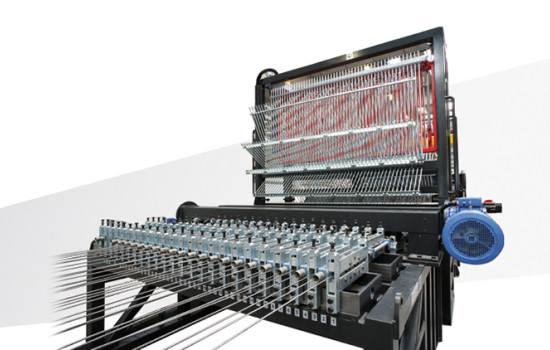
P Weld
ELECTRO-WELD MESH MACHINE FROM COIL P Weld (mesh sheets)
LW ∅3.4 – 8 mm (#2)
CW ∅3.4 – 8 mm (#2)
Single welding unit: enables the production of panels.
Production flexibility: the ability to choose from various output configurations to meet specific production needs.
Optional stacking system: automates the handling and positioning of P Weld panels, optimizing workflows and finished product storage.
Optional panel turner: optimizes the stacking height of P Weld panels.
Optional automatic tying machines: automate the tying process, ensuring greater efficiency and safety.

C Weld
ELECTRO-WELD MESH MACHINE FROM COIL C Weld (mesh rolls)
LW ∅3.4 – 6 mm (#2)
CW ∅3.4 – 6 mm (#2)
Produces electro-welded mesh coils: manufactures rolls of electrically welded metal mesh.
Thin wire: works with wire up to 6 mm in diameter.
Fully automatic process: manages all stages autonomously, from wire feeding to finished coil creation.
High-speed production: designed to maximize output.
Versatile wire input: accepts both cold drawn and hot rolled, smooth or ribbed wire.
Precise welding: utilizes multiple transformers to ensure uniform current distribution and impeccable welds.
Automatic coil handling: cuts, evacuates, and stacks coils automatically, reducing operator workload.
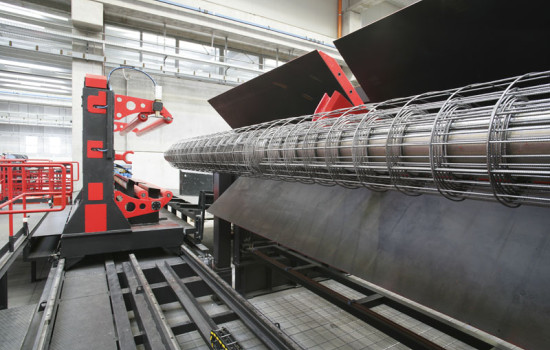
C TwinWeld
ELECTRO-WELD MESH MACHINE FROM COIL C Twin Weld (mesh rolls)
LW ∅3.4 – 6 mm (#2)
CW ∅3.4 – 6 mm (#2)
Twin welding unit: employs two welding units for simultaneous cross wire positioning and welding.
Doubled production speed: achieves nearly double production rate due to faster longitudinal wire advancement.
Fully automated: encompasses wire feeding, positioning, welding, and cutting.
High-speed production: designed for maximum output.
Precise welding: utilizes multiple transformers for uniform current distribution.
Automated coil handling: includes automatic cutting, evacuation, and stacking of coils.
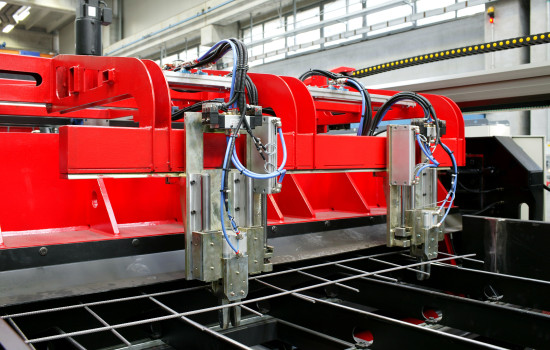
P TwinWeld
ELECTRO-WELD MESH MACHINE FROM COIL P Twin Weld (mesh sheets)
LW ∅3.4 – 8 mm (#2)
CW ∅3.4 – 8 mm (#2)
Twin welding unit: employs two welding units for simultaneous cross wire positioning and welding.
Doubled production speed: achieves nearly double production rate due to faster longitudinal wire advancement.
Fully automated: encompasses wire feeding, positioning, welding, and cutting.
High-speed production: designed for maximum output.
Precise welding: utilizes multiple transformers for uniform current distribution.
Automated panel handling: includes automatic panel evacuation and stacking.